
Dock scheduling is the assignment of time slots and dock doors to trucks that come to pick up or drop off goods at a facility.
It’s one of the most overlooked processes in logistics. The way it’s handled has a quietly major effect on warehouse and transportation performance, on a company’s ability to collect and analyze data about its supply chain, and ultimately on customer satisfaction.
Many facilities operate on a strictly first-come-first-served basis. If that sounds familiar, our primer on time slot management shows how even a simple appointment grid can be a game-changer for teams still living in the FCFS world.
Even more common is to agree on time slots with carriers, in the full knowledge that many loads will come unscheduled, and the majority will arrive hours before or after their scheduled time, if they even make it on the same day.
But the most successful operations use software to manage the process, collect data, and hold carriers accountable.
What Supply Chain Executives Should Know about Dock Scheduling

COOs and VPs of Supply Chain are often unaware of the outsized impact of loading dock operations on overall logistics performance, not to mention the untapped source of data to be found there.
What looks like a niche area of warehouse operations is really:
- One of the biggest contributors to warehouse workforce churn and productivity problems.
- A major area of cooperation or contention with suppliers and transportation providers.
- The site at which most inventory shrinkage has its root cause.
- An enabler, or roadblock, to visibility and data-driven operations.
If it’s so important, why haven’t mid-level managers taken care of it? Probably because it has some of the attributes of a wicked problem. Namely: internal and external stakeholders that cannot communicate their true objectives and capabilities to each other accurately enough. Fear of opening a can of worms. Underestimating the benefits of decisive action and change.
The good news is that these stakeholders also tend to overestimate the difficulty. Facilities that do adopt specialized dock scheduling software are overwhelmingly positive about the results, both in terms of meeting KPIs and the subjective impact on quality-of-life.
Few dock scheduling projects are carried out at the group level. Best-in-class dock scheduling software is almost always delivered as SaaS, with minimal input from IT. It’s not uncommon to see different facilities belonging to the same company using competing products from different vendors!
But that might soon change. As COOs and VPs turn their attention to issues with labor, shrinkage, supply chain collaboration and visibility, their strategic investigations are increasingly pointing them towards the loading dock.
Curious how your operation stacks up? Use our five-stage loading dock maturity model to benchmark your situation today and map out your next level of capability.
What Warehouse Managers Should Know About Dock Scheduling
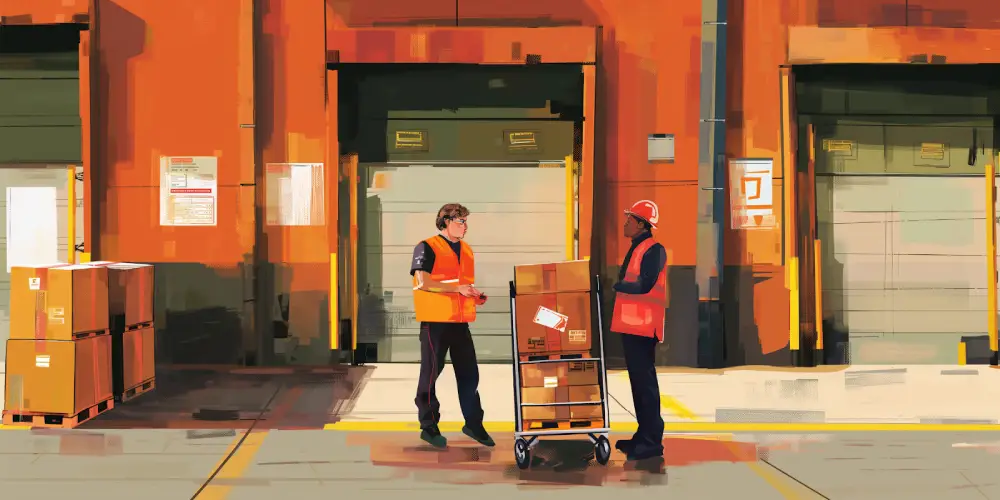
In the warehouse, you’re trying to keep costs low, inventory accuracy high, and orders processed as quickly as possible.
The traditional assumption is that putaway, storage, picking and packing have a lot of potential for optimization, while shipping and receiving is largely out of your control. We often see reactive labor allocation, with overstaffing during slow periods and understaffing during peaks, not to mention dependence on overtime and temporary staffing agencies.
One important question is whether to make use of specialist unloading services or rely entirely on your in-house team. Our deep dive into pros and cons of third-party “lumper” crews breaks down the cost, speed, and risk trade-offs.
Since shipping and receiving is time-sensitive, the arrival of an unexpected truck can throw off your plan for the day. And when warehouses are overwhelmed, the loading dock is often the first place where standards drop. More accidents and injuries happen there than in any other part of the warehouse, and it’s where mishandling, damage and theft is most likely to occur.
But what if it’s possible to take control of the schedule? Of course, this requires the cooperation of carriers. So how do you convince them to cooperate?
The answer is data. And the first step is eliminating the friction for them. What works for some facilities is telling carriers: from now on we won’t accept any truck without an appointment. It doesn’t matter if it comes 6 hours late, as long as it’s in the system. And here’s the link where you can book your slot online. No calls or emails necessary.
What happens next is business as usual. Trucks continue to turn up whenever they turn up, throughout the day. Every now and then a truck turns up pretty close to its scheduled time, and whenever that happens you direct your team to work that load right away. For each truck, your coordinator is recording the arrival time and departure time.
As this data accumulates, it becomes a tool for negotiation and improvement. You provide feedback to carriers, showing them how punctuality gets their drivers back on the road faster. They gradually improve their own practices to benefit from this system. Meanwhile, you can refine your labor allocation, reducing both downtime and costs.
Sooner or later, you see a marked improvement across warehouse operations as a whole.
What Transportation Professionals Should Know About Dock Scheduling
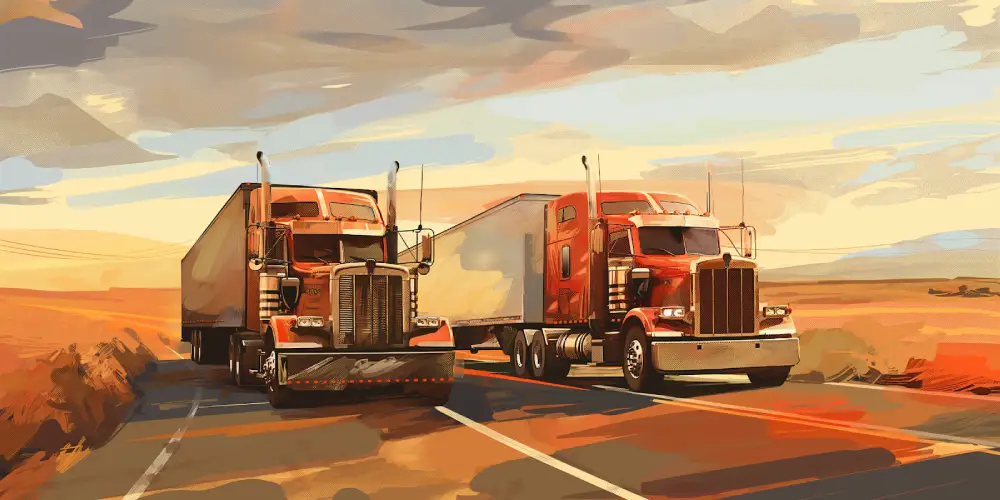
Good scheduling practices make your operations more attractive to carriers. Carriers prefer working with facilities that provide predictable and efficient loading/unloading times as it helps them plan better routes and schedules. This reliability can lead to more favorable shipping rates and improved service levels from your carriers.
Data gathered from well-managed dock scheduling systems provides you with insights into carrier performance and operational bottlenecks. This information is invaluable for strategic planning, allowing you to negotiate better terms with carriers and arrange more balanced schedules.
With access to real-time and historical data, logistics managers can also foresee potential delays associated with specific carriers, load types, or even environmental conditions. Recognizing these trends enables you to adjust plans in advance, shifting from a reactive to a proactive approach.
Spreadsheets Versus Dock Scheduling Software
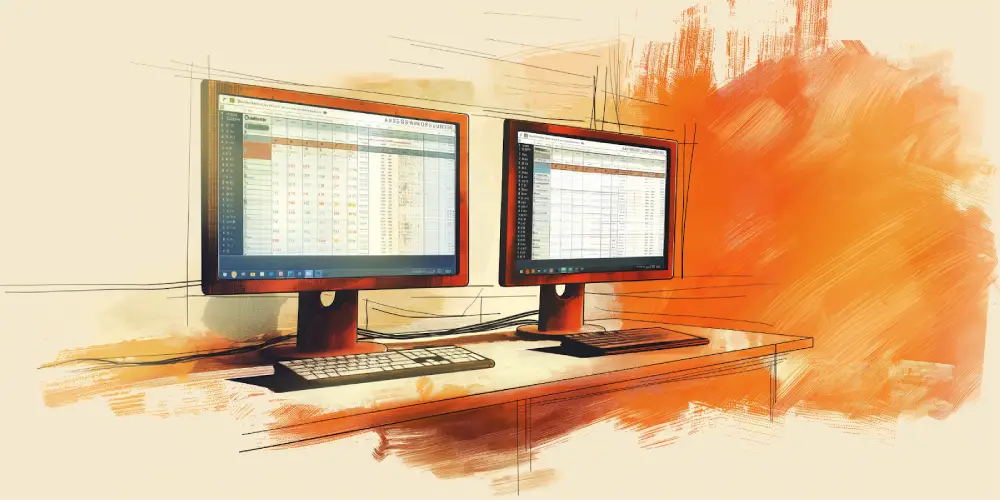
A logistics clerk with a telephone and a whiteboard can do dock scheduling. But the tools they have access to can multiply the control they exert over the schedule.
The typical setup is an excel spreadsheet stretched to its limits, an overflowing email inbox, and a heroically hard-working coordinator with a world class memory holding it all together. If they come down with the flu, it’s over for any semblance of order and calm in the loading dock.
Then we have entry-level dock scheduling systems where carriers can self-serve appointments online, but offer less customizability than a spreadsheet. This configuration can take some pressure off the coordinator, but they’ll still spend most of their day on calls and emails. Data collection will be limited, and not consistent enough for real analytics or insights.
Finally there’s DataDocks, which gives you an advanced algorithm that allocates appointments based on what makes sense for the facility, sends automatic notifications when either party needs to change the schedule, and gives you as much control and data capture as you need.
Complex distribution centers face extra variables—multiple simultaneous doors, wave-based shifts, and higher truck counts—so we’ve detailed how to handle those in our guide on appointment management for large DCs.
Dock Scheduling Versus Similar Software
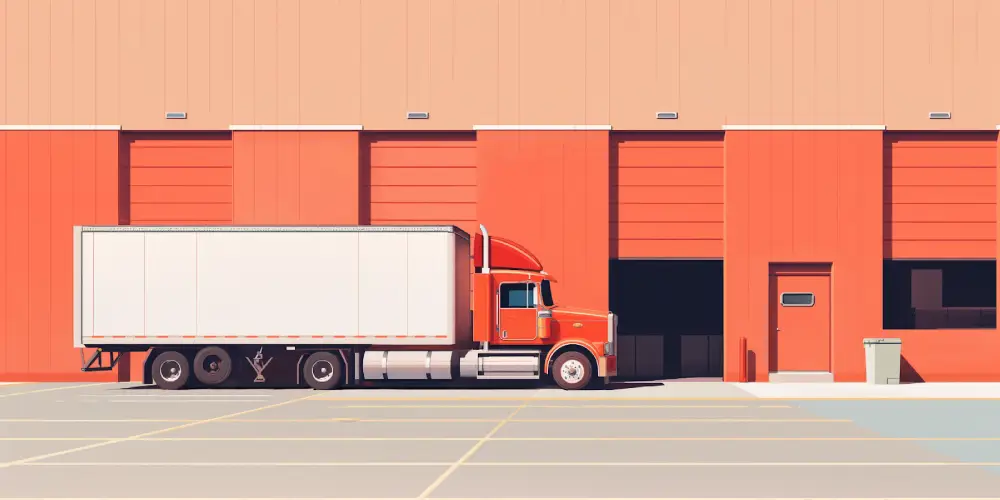
Does your TMS/WMS/SCMS Include Dock Scheduling?
Almost all modern logistics software suites offer some kind of ‘dock scheduling’ module. In most cases they offer less functionality than a well-designed excel spreadsheet. A handful include some kind of carrier booking portal, which might be on par with generic appointment scheduling software.
A dedicated dock scheduling system is not designed to replace your WMS or any other part of your software stack. All the market leaders offer integration with other systems as a core feature, and DataDocks goes the extra mile to make sure you get the value you’re hoping for from such integrations.
Is Dock Scheduling the same as a Delivery Scheduling System or Truck Scheduling Software?
No. These tools, also often known as dispatch or route planning systems, are the carrier counterpart to dock scheduling systems. They allow fleet operators to keep track of their trucks while they’re on the road, and optimize routes based on the best fuel economy, speed, or in the case of LTL operations, to maximize average capacity utilization.
A full-featured TMS or Fleet Management System will include similar functionality.
It’s also possible to connect a carrier’s dispatch system to a facility’s dock scheduling system via API. This would allow the two logistics coordinators at each company to exchange data, request changes to the schedule and provide updates without leaving their ‘native’ system, which could be helpful for optimal productivity.
Is Dock Scheduling the same as a Carrier Appointment System?
Yes. “Carrier Appointment System” is a term that was used in the early days of dock scheduling software.
Some legacy software still uses the name Carrier Appointment System. For example, the United States military’s Transportation Command maintains a proprietary dock scheduling system called CAS.
Is Dock Scheduling the same as Truck Booking Software?
No. Truck Booking Software usually refers to an extremely lightweight TMS or load board, especially in developing countries. It can also sometimes be a synonym for dispatch software.
A number of mobile apps now exist that aim to offer an ‘uber-like’ experience for small businesses who occasionally need to arrange their own freight. However, most of the leading TMS providers have their own mobile apps and are likely to remain the preferred solution for any business looking to automate freight purchasing.
Is Dock Scheduling the same as Yard Management?
There can be significant overlap between dock scheduling and yard management, but they’re not the same thing.
Yard management is a big umbrella that covers all of the operations and asset control that takes place in a facility’s exterior. When that facility is a warehouse, or otherwise gets a lot of truck traffic, then those operations are going to be intimately tied to dock scheduling.
Container terminals, construction sites, and maintenance depots all have their own kinds of yard management software. These environments don’t always have loading docks, and even when they do, they tend to form a small part of yard operations.
But for facilities that have a busy loading dock, yard management is really an extension of dock scheduling. Some yard management software might include some basic dock scheduling features, but DataDocks integrates the two seamlessly.